Accelerate Productivity in 2025
Reignite Growth Despite the Global Slowdown
Poorly maintained manufacturing assets lead to excessive interruptions and downtimes in production lines. The industrial internet of things (IIoT) and maintenance analytics facilitate real-time monitoring and timely fault detection. This data supports predictive maintenance, enabling factories to identify potential failures before they occur, thus reducing repair costs. Routine and hazardous maintenance tasks often expose workers to high-risk environments.
This industry research highlights the top 10 industrial maintenance trends that enhance workplace safety, boost productivity, and lower maintenance costs. These trends include immersive technologies, human-machine interfaces (HMIs), 3D printing, and maintenance-as-a-service (MaaS). Read on to explore all trends and learn how they can impact your production lines.
Top 10 Industrial Maintenance Trends in 2025
- Industrial Internet of Things
- Predictive Maintenance
- Maintenance Analytics
- Immersive Technologies
- Maintenance Robotics
- Digital Twin
- 3D Printing
- Maintenance-as-a-Service
- Human-Machine Interfaces
- Green Maintenance
Methodology: How We Created the Industrial Maintenance Trend Report
For our trend reports, we leverage our proprietary StartUs Insights Discovery Platform, covering 5M+ global startups, 20K technologies & trends plus 150M+ patents, news articles, and market reports.
Creating a report involves approximately 40 hours of analysis. We evaluate our own startup data and complement these insights with external research, including industry reports, news articles, and market analyses. This process enables us to identify the most impactful and innovative trends in the industrial maintenance sector.
For each trend, we select two exemplary startups that meet the following criteria:
- Relevance: Their product, technology, or solution aligns with the trend.
- Founding Year: Established between 2020 and 2025.
- Company Size: A maximum of 200 employees.
- Location: Specific geographic considerations.
This approach ensures our reports provide reliable, actionable insights into the industrial maintenance innovation ecosystem while highlighting startups driving technological advancements in the industry.
Innovation Map outlines the Top 10 Industrial Maintenance Trends & 19 Promising Startups
For this in-depth research on the Top 10 Industrial Maintenance Trends & Startups, we analyzed a sample of 664 global startups & scaleups. This data-driven research provides innovation intelligence that helps you improve strategic decision-making by giving you an overview of emerging technologies in the maintenance industry. In the Industrial Maintenance Innovation Map, you get a comprehensive overview of the innovation trends & startups that impact your company.
These insights are derived by working with our Big Data & Artificial Intelligence-powered StartUs Insights Discovery Platform, covering 4.7M+ startups & scaleups globally. As the world’s largest resource for data on emerging companies, the SaaS platform enables you to identify relevant technologies and industry trends quickly & exhaustively.
Tree Map reveals the Impact of the Top 10 Industrial Maintenance Trends
Based on the Industrial Maintenance Innovation Map, the Tree Map below illustrates the impact of the Top 10 Industrial Maintenance Trends in 2025. Startups and scaleups leverage IIoT, predictive and preventive maintenance, and advanced analytics to address the malfunction before it occurs.
Further, companies develop maintenance analytics and HMI systems for data-driven maintenance in factories and manufacturing units. Robotics-driven automation streamlines maintenance operations and aids the delivery of maintenance as a service. Lastly, digital twins and immersive technologies improve data visualization and worker training while green maintenance improves the sustainability of maintenance operations.
Global Startup Heat Map covers 664 Industrial Maintenance Startups & Scaleups
The Global Startup Heat Map showcases the distribution of 644 industrial maintenance exemplary startups and scaleups analyzed using the StartUs Insights Discovery Platform. It highlights high startup activity in the US and India, followed by Western Europe. From these, 20 promising startups are featured below, selected based on factors like founding year, location, and funding.
Want to Explore Industrial Maintenance Innovations & Trends?
Top 10 Industrial Maintenance Trends in 2025
1 Industrial Internet of Things
IIoT refers to the integration of the internet of things (IoT) into industrial processes and systems. This enables real-time data collection on the performance and condition of industrial equipment.
Startups leverage this data and apply advanced data processing algorithms to enable prior scheduling of maintenance, which reduces the risk of equipment failure and downtime. IIoT-sourced data also allows manufacturing businesses to analyze and identify asset anomalies to enable data-driven decision-making in maintenance.
Moreover, it enables remote monitoring and diagnosis of problems in the equipment, reducing the need for on-site maintenance. Various stakeholders that benefit from IIoT include maintenance teams, equipment manufacturers, operators, and facility managers, improving asset tracking and overall equipment effectiveness (OEE).
The global industrial IoT market size is estimated at USD 438.90 billion in 2024 and is anticipated to reach around USD 2146.07 billion by 2034, expanding at a compound annual growth rate (CAGR) of 17.20% from 2024 to 2034.
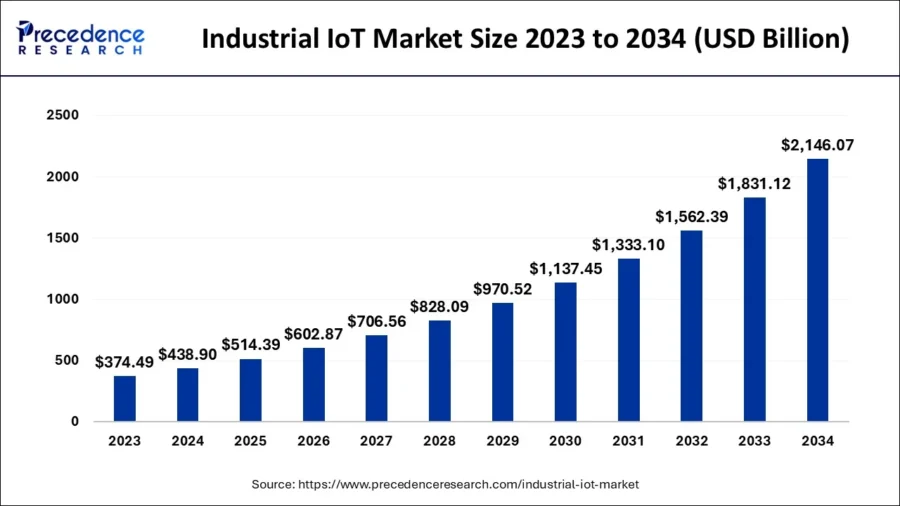
Credit: Precedence Research
BREN TECHNOLOGIES develops AI-enabled Smart Sensors
Turkish startup BREN TECHNOLOGIES makes AI-enabled smart sensors. The startup’s steam efficiency monitoring system, BREN STM, continuously monitors traps to identify steam leaks that lead to other equipment failures.
Likewise, the startup’s solution for heat exchanger monitoring, BREN HEM, identifies failures and leakages using AI. Additionally, BREN TECHNOLOGIES’ companion platform allows plants to manage the startup’s products. Chemical and energy industries leverage the startup’s IIoT-enabled devices to enhance industrial data acquisition and enable predictive maintenance.
Bufo Innovations offers Smart Maintenance Sensors
Indian startup Bufo Innovations develops smart maintenance sensors. The startup’s hardware and software suite includes a wireless vibration analyzer and current sensors that capture and diagnose equipment issues using AI.
Its platform allows businesses to connect industrial assets to cloud or on-premise deployments using low-range wide area networks (LoRAWAN) or narrow-band IoT (NB-IoT). This makes data acquisition more efficient and mitigates in-house product development for factories. The startup’s AI-based condition monitoring allows them to identify anomalies and receive automated alerts upon detecting anomalies.
2. Predictive Maintenance
Integrating big data and advanced analytics into asset data enables predictive maintenance for factories to forecast equipment conditions and failures.
As part of proactive maintenance, sensors and cameras record large sets of data on temperature, vibrations, and conductivity, among others. Such solutions then transmit the data to software platforms to identify anomalies using AI and machine learning algorithms.
Industrial asset management teams leverage this technology to estimate when maintenance should be performed, thereby allowing asset replacement or repair before failure.
The global market for the predictive maintenance market is projected to grow from USD 10.6 billion in 2024 to USD 47.8 billion in 2029, at a CAGR of 35.1% during the forecast period.
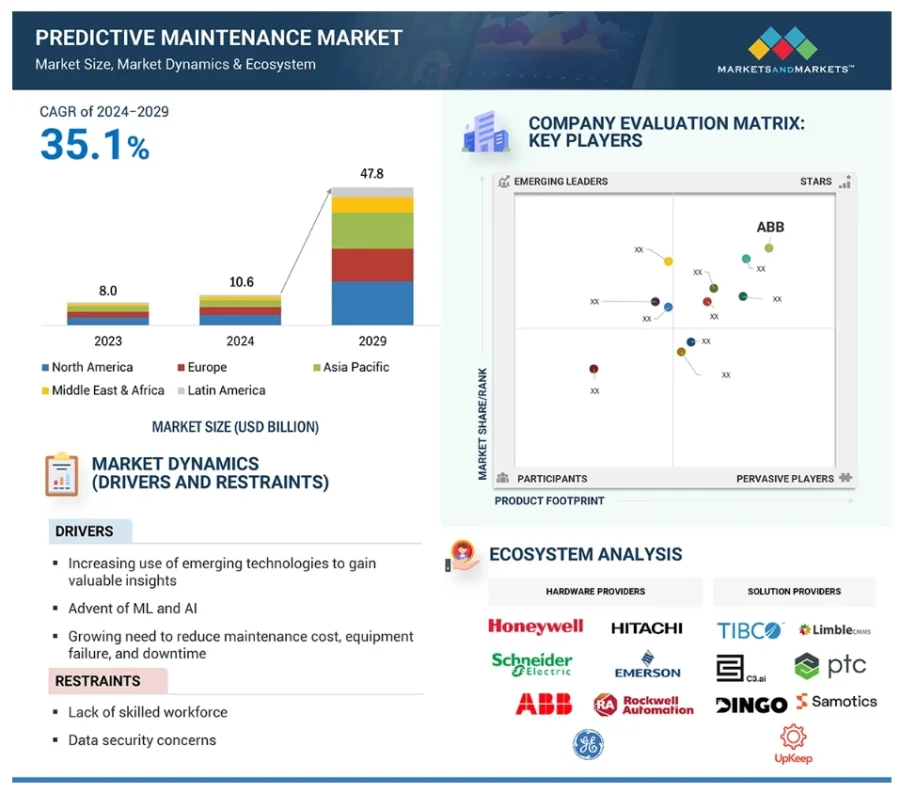
Credit: Markets and Markets
Feelit delivers Anomaly Detection Analytics
Israeli startup Feelit offers anomaly detection analytics for predictive maintenance. The startup collects data using a nanotechnology-powered sensor and an edge device. They analyze the collected data using artificial intelligence to identify structural and parameter changes in machinery to provide actionable insights.
Asset operators utilize the startup’s solution for integrating non-intrusive condition monitoring in factories.
NovoAI provides Acoustic & Vibration Analysis
US-based startup NovoAI makes acoustic and vibration analytics devices. The startup’s products, AVA and TESS, constantly measure the equipment conditions such as defects, internal imperfections, etc., using vibrations and acoustics.
Using the startup’s AI and high-speed vision systems, production units predict equipment failures remotely. The startup then delivers the data through an easy-to-understand intelligent dashboard, aiding maintenance planning.
3. Maintenance Analytics
Maintenance analytics is a rapidly advancing trend within industrial maintenance that employs advanced data analysis techniques to optimize equipment maintenance and minimize downtime.
One prevailing trend in maintenance analytics is the integration of data from heterogeneous sources, such as sensors, equipment logs, and maintenance records, to obtain a more holistic view of equipment health and performance.
Moreover, there is a growing interest in utilizing this data to provide remote assistance and training for maintenance technicians. Finally, cloud-based analytics platforms are gaining traction as they facilitate real-time monitoring and analysis of equipment performance data while also enabling informed decision-making.
Groundup.ai offers Condition-based Integrated Maintenance
Ghana-based startup Groundup.ai provides condition-based integrated maintenance using data-driven software, IoT, and computer vision. The startup remotely carries out a sound diagnosis of machinery using sensors and identifies unique frequency profiles using AI.
It compares the noise across different periods and instantly notifies plant operators of any anomalies. This enables the heavy machinery and logistics industries to perform reactive maintenance, thereby improving the mean time between failures.
Edge Impulse makes a Machine-embedded Platform
US-based startup Edge Impulse develops a machine-embedded platform. It utilizes computer vision and sensors to collect audio data and automatically identify dangerous conditions and machine failures.
The platform also proactively performs maintenance and sends automated sound alerts to production process engineers in case of anomalies. This ensures always-on assembly lines, increasing throughput.
4. Immersive Technologies
Immersive reality technologies, such as virtual reality (VR) and augmented reality (AR), improve industrial maintenance in several ways. For example, these technologies create interactive training environments and help technicians troubleshoot problems more efficiently and accurately.
In particular, AR superimposes instructions or diagrams onto the equipment, making it easier for technicians to follow procedures and locate components. Companies also create 3D models of equipment and facilities to visualize and optimize maintenance schedules and procedures.
Moreover, remote assistance using AR and VR delivers on-demand expert guidance and support from a distance to the maintenance technicians. Despite the cost of immersive technologies, companies invest in these technologies to improve the performance of maintenance technicians and reduce the risk of accidents.
The global immersive technology market size is anticipated to reach around USD 250.96 billion by 2034, expanding at a CAGR of 22.30% from 2024 to 2034.
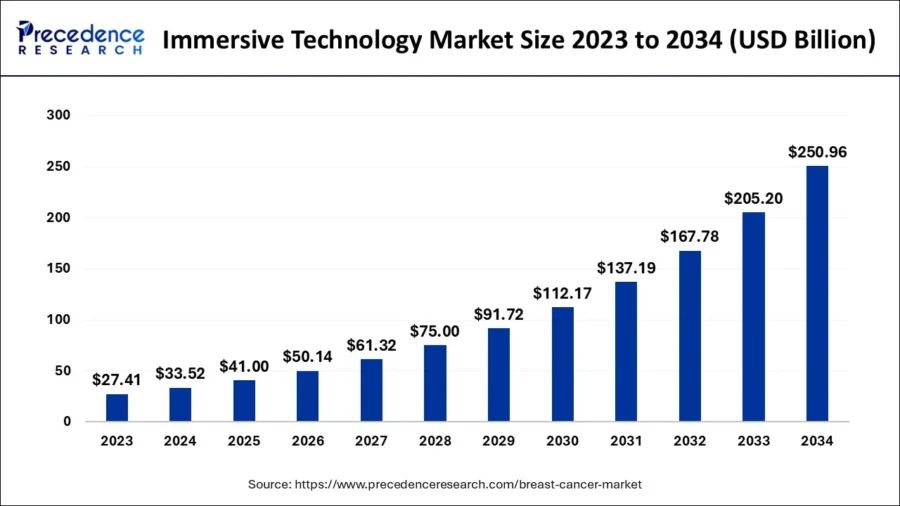
Credit: Precedence Research
I-sense develops Industrial AR
Maltese startup I-sense creates industrial AR solutions. The startup collects sensor data and displays it in AR environments using smart glasses. This enables step-wise visualization and simulation of maintenance operations.
Maintenance operators and inspectors leverage this technology to obtain 3D models of scanned assets and locate equipment to support easy maintenance.
Virtual X offers VR-based Maintenance Training
Virtual X is a Malaysian startup that provides VR-based maintenance training. The startup’s cloud VR-based platform tracks maintenance training data. It supports heavy manufacturing units and factory operators to remotely manage the training process. The oil and gas (O&G), energy, and aviation industries rely on this technology to introduce risk-oriented virtual training, improving new employee performance.
5. Maintenance Robotics
The use of robotics in maintenance operations offers benefits such as better efficiency, reduced costs, and improved safety. For instance, collaborative robots or cobots work alongside human technicians to perform maintenance tasks.
Companies also leverage autonomous mobile robots (AMRs) that navigate through facilities and perform routine maintenance tasks like cleaning, inspection, and data collection, without human intervention. Additionally, there is a growing interest in the use of drones for maintenance inspections in hard-to-reach areas like oil rigs and manufacturing plants.
The service robotics market is projected to grow from USD 47.1 billion in 2024 to USD 98.65 billion in 2029, growing at a CAGR of 15.9%.
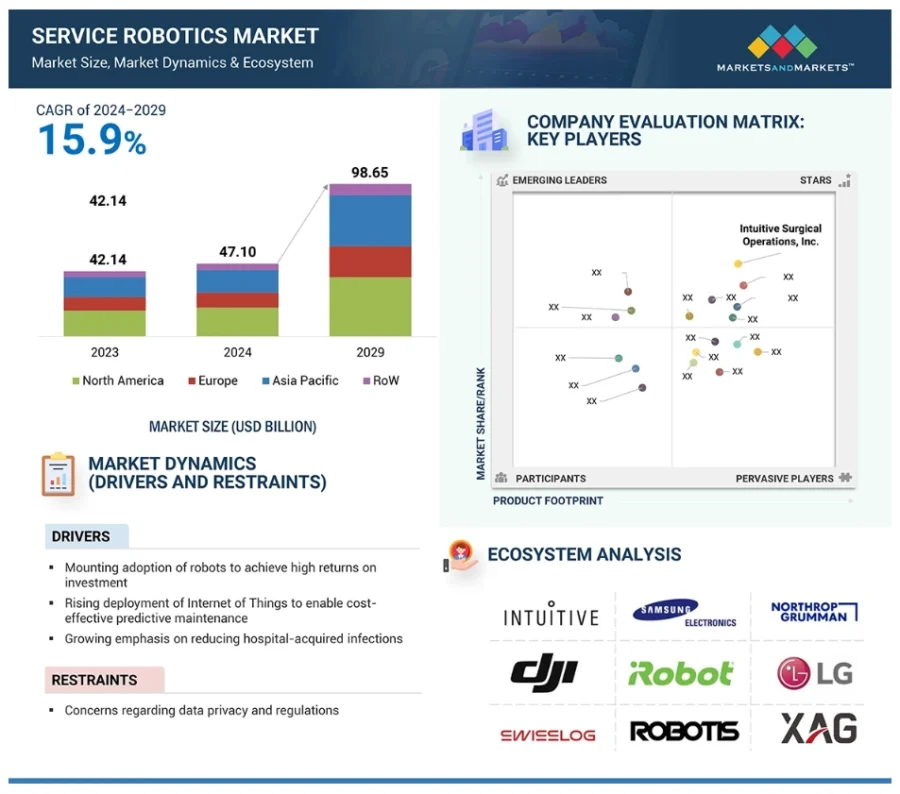
Credit: Markets and Markets
BRISTOLA manufactures Submersible Cleaning Robots
BRISTOLA is a US-based startup that makes submersible cleaning robots. These remote-controlled robots go through the entry box and clean the tanks of sediment and build-up. The robots also monitor facility conditions and performance to maintain and keep liquid storage facilities healthy.
Companies leverage the startup’s robots to automate facility maintenance while improving workplace safety.
6. Digital Twin
In the context of industrial maintenance, startups leverage digital twins to simulate and analyze the equipment or production line performance in real time. This improves the reliability, efficiency, and effectiveness of manufacturing operations.
By analyzing the simulated data, it is possible to determine the optimal intervals for performing maintenance tasks, such as inspections, repairs, or replacements. This reduces intervention frequency, which saves time and money while also improving OEE.
Further, digital factory twins aid virtual, interactive, and customized training for maintenance technicians. Such environments allow maintenance technicians to practice and learn new skills in a safe, simulated, yet real-world environment.
Digital twins can reduce maintenance costs by up to 40% while increasing equipment uptime by as much as 10%
The global digital twin market size is predicted to reach around USD 471.11 billion by 2034, expanding at a CAGR of 37.29% from 2025 to 2034.
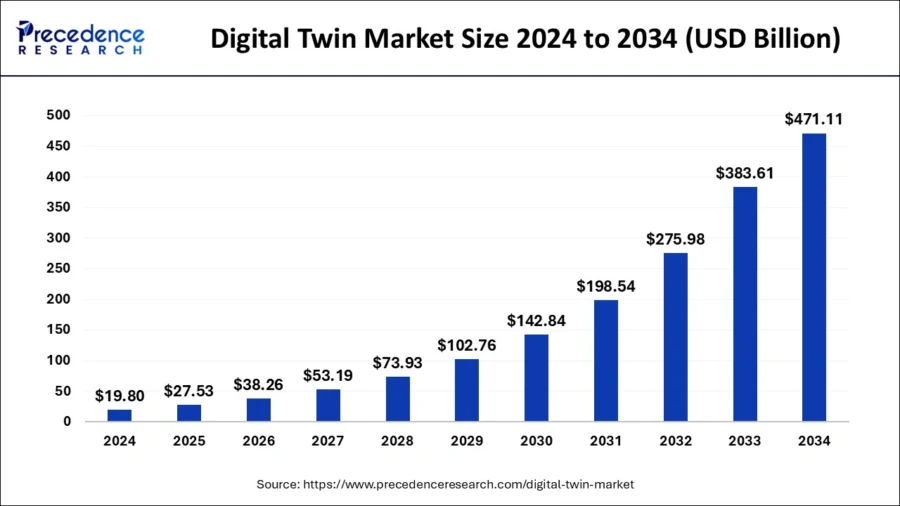
Credit: Precedence Research
Ris3d builds an Industrial Animation App
Brazilian startup Ris3d specializes in digital twins and 3D modeling for industrial facilities and complex infrastructures. The technology combines 3D laser scanning technology with modeling and artificial intelligence to create accurate digital representations of physical environments. The process involves capturing up to 2 million points per square meter using laser scanners, followed by 3D modeling and integration with augmented reality AI.
This solution provides industrial layout optimization, predictive maintenance, safety simulations, asset management, and renovation planning. It is suitable for industries like oil and gas and manufacturing, as well as engineers, facility managers, and safety teams.
3i simplifies Remote Asset Monitoring
South Korean startup 3i enables remote asset monitoring. The startup’s solution, Beamo, captures entire factory or production site data in an immersive 360-degree environment and visualizes the IoT system through a digital twin.
This enables industry experts, consultants, and technicians to obtain real-time data while also providing insights into asset conditions. Maintenance managers integrate this technology in various industries for improving visibility into maintenance activities.
7. 3D Printing
3D printing, or additive manufacturing, enables the production of custom parts quickly and cost-effectively. Startups are developing high-performance materials, such as carbon fiber-reinforced polymers, to produce parts that withstand high stress and extreme conditions. This also results in the integration of 3D printing with other maintenance technologies, such as drones and sensors, to streamline maintenance operations and reduce downtime.
On-demand spare parts production also reduces lead times and inventory costs. Portable 3D printers further aid on-demand production by reducing the need for expensive downtimes and transportation for on-site emergency repairs.
The global 3D printers market is expected to reach around USD 119.92 billion by 2034, expanding at a CAGR of 17.3% from 2024 to 2034.
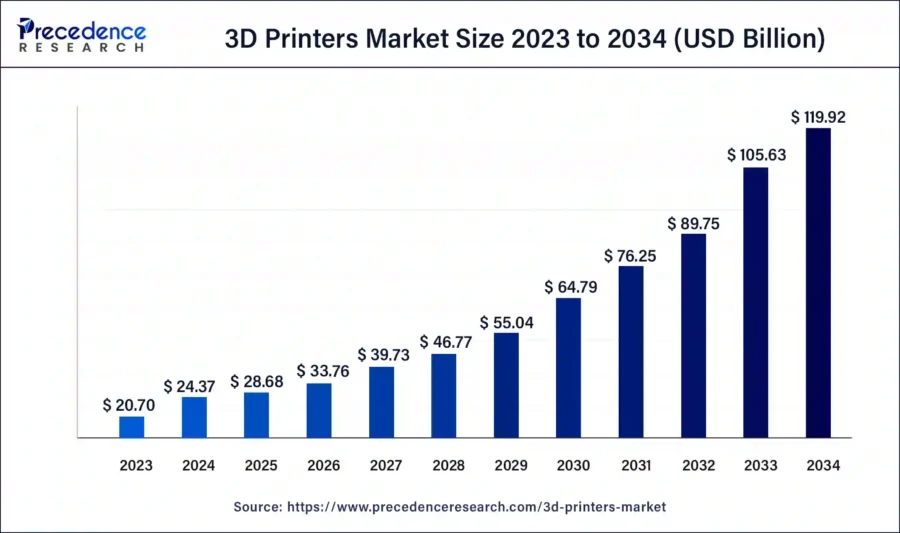
Credit: Precedence Research
MELD Manufacturing offers Single-Step 3D Printed Metal Parts
MELD Manufacturing is a US-based startup that offers single-step 3D-printed metal parts. The startup uses a solid-state process, MELD, wherein the material does not reach the melting temperature during the process. As a result, it enables high-quality parts with low residual stress.
The metal additive market leverages the low-power consumption capability of this technology to manufacture aluminum, titanium, and steel-based spare parts for maintenance on demand.
Procada develops Material Deposition 3D Printing
Swedish startup Procada provides material deposition 3D printing technology. The startup uses a direct energy deposition (DED) additive manufacturing process that uses a laser or plasma arc to melt the feedstock material.
It then deposits these materials layer after layer in the form of solidified beads to obtain 3D shapes. Metal manufacturing industries utilize the startup’s technology to repair worn parts or fabricate new parts.
8. Maintenance-as-a-Service
The high cost of predictive maintenance makes it unaffordable for small and medium-sized enterprises (SMEs). To maintain the quality and cost efficiency of maintenance operations, they leverage the services of companies that offer maintenance-as-a-service.
SMEs also get the advantage of subscription models that balance the cost of maintenance. Moreover, maintenance equipment manufacturers benefit from additional business opportunities by ensuring recurring revenue. These services include software solutions such as computerized maintenance management systems (CMMS) and hardware solutions that include robots and other equipment like safety gear.
Further, startups and scaleups provide services such as periodic calibration and lubrication services.
The global industrial maintenance services market is set to reach USD 76.96 billion by 2029 at a CAGR of 7.3%.
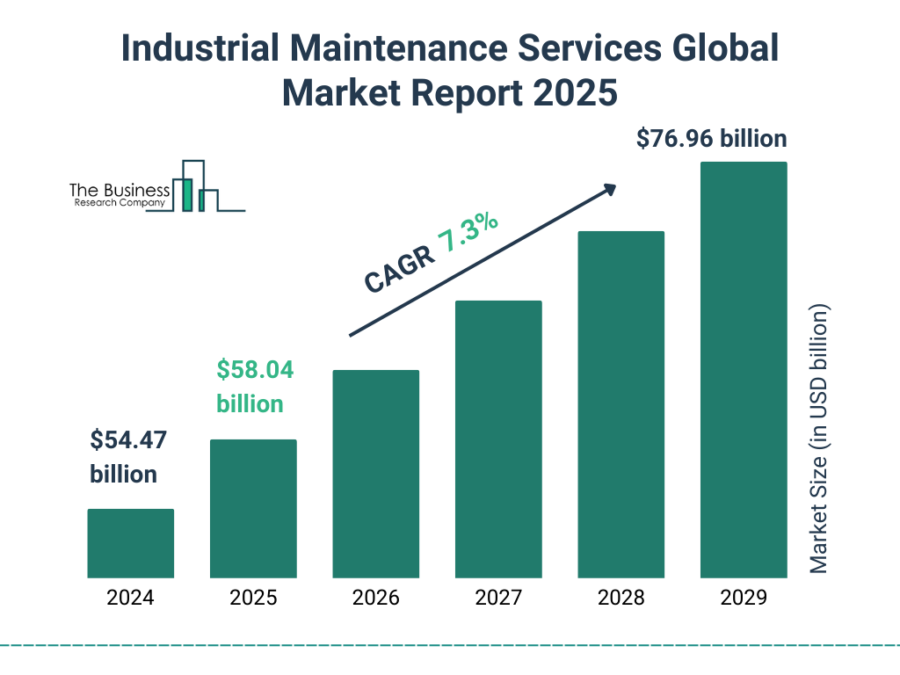
Credit: The Business Research Company
sFIX develops a Computerized Maintenance Management System
German startup sFIX makes a computerized maintenance management system. The startup’s CMMS app integrates into existing industrial systems to digitize maintenance and documentation.
By scanning QR codes on machines, operators are able to quickly access maintenance logs and all documentation, making spare part procurement effective. Since the startup’s solution is digitized and features centralized data, it allows factory operators to improve maintenance planning and leverage preventive maintenance.
MAB Robotics makes Legged Inspection Robots
MAB Robotics is a Polish startup that develops legged inspection robots. The startup’s quadrupedal robot, Honey Badger, features multiple cameras and sensors as well as being deployable in hostile environments.
MAB Robotics leverages Honey Badger to deliver inspection as a service (IaaS) to the utility sector. This allows water and sewage maintenance technicians to replace workers from high-risk situations and accelerate periodic inspections.
9. Human-Machine Interfaces
An HMI is a user interface that allows operators to interact with and control industrial machinery and equipment. Factories and manufacturing plants implement HMIs through various methods, such as dedicated control panels, touchscreen displays, and mobile devices. They feature alarms, alerts, and data logging to help operators monitor and manage equipment performance.
Through these features, HMIs improve the efficiency and effectiveness of industrial maintenance by providing real-time data and diagnostic information. Further, the integration of artificial intelligence (AI), machine learning (ML), and cloud-based HMIs provides operators with actionable insights and recommendations.
This enables real-time collaboration, data sharing between multiple users, and remote maintenance.
The global human-machine interface market is anticipated to reach around USD 18.36 billion by 2034, growing at a CAGR of 10.60% between 2024 and 2034.
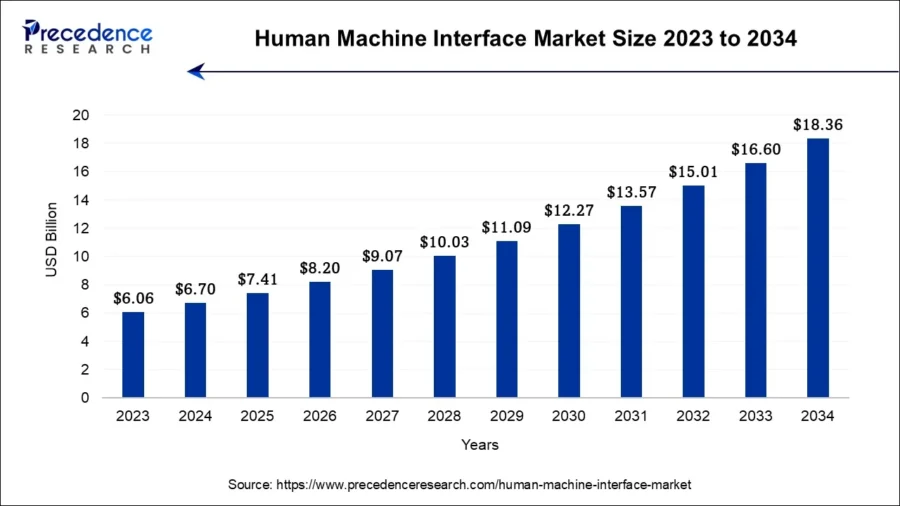
Credit: Precedence Research
ADISRA develops Smart HMI Software
US-based startup ADISRA offers ADISRA SmartView 4.0, an HMI/SCADA package for developing applications for monitoring and managing machines and plants. The startup integrates communication drivers with various modules and devices.
The startup’s cloud-based OEE and analytics platform, ADISRA InsightView, reduces equipment downtimes and improves equipment lifecycle management. Additionally, another cloud-based system, ADISRA KnowledgeView, anticipates maintenance requirements, aids fault diagnosis, and increases machinery mean time between failures (MTBF). These solutions allow manufacturers to create digitized smart factories.
IoTize offers Mobile HMI Modules
IoTize is a French startup that provides mobile HMI modules. The startup’s TapNLink wireless modules offer a secure and configurable connection port for mobile devices. This enables the creation of customizable mobile HMI apps.
These mobile apps improve the visibility of key maintenance parameters and data to streamline on-site maintenance for manufacturing units.
10. Green Maintenance
In industrial operations, green maintenance involves adopting environmentally sustainable practices for maintaining equipment and facilities. This includes utilizing renewable energy sources like solar or wind power for running machinery and facilities.
Maintenance teams leverage techniques like vibration analysis and thermal imaging to identify potential equipment failures, reducing waste and energy consumption. Startups are also focusing on the proper disposal of hazardous materials and sustainable waste management practices.
For this, manufacturers leverage eco-friendly lubricants, adopt energy-efficient lighting systems, and install water conservation systems. Adopting these practices allows them to reduce the environmental impact of industrial maintenance operations while also enhancing efficiency and reducing costs
MAVEN GREENTECH simplifies Air Filter Diagnostic Cleaning
MAVEN GREENTECH is an Australian startup that offers on-site air filter diagnostic cleaning and integrating testing technology. The startup’s product, AirX, utilizes a patented dry cleaning process with a triple nozzle compressed airhead to clean large diesel engine filters.
It also analyzes the filter before and after dust removal in a diagnostic chamber. The filter is unfit for use if it does not meet ISO standards or visual inspection. The mining and construction industries leverage this technology to identify optimal reuse ability and underperforming filters to shorten fleet downtime and reduce air filter-related costs.
Ecochem manufactures a Sustainable Industrial Degreaser
Ecochem is an Indian startup that provides Eco-Green Kleen, a sustainable industrial degreaser. Unlike conventional industrial cleaning products, the startup leverages a water-based formulation to eliminate the use of toxic chemicals.
Eco-Green Kleen works on oil, grease, paint, and other chemical stains to clean heavy machinery. That is why factories, mines, and refineries utilize Ecochem’s cleaning solution, reducing the environmental impact of maintenance activities.
Discover all Industrial Maintenance Trends, Technologies & Startups
The use of wireless, internet-enabled technologies, including connected industrial control systems and 5G, changes the way industrial maintenance teams work. Since manufacturers and factory operators are moving towards the establishment of smart factories and Industry 4.0, IIoT will continue to support asset repairs and maintenance efforts. This data also powers technologies like computer vision and deep learning to better inspect and maintain hard-to-reach equipment. The industrial maintenance trends & startups outlined in this report only scratch the surface of trends that we identified during our data-driven innovation & startup scouting process. Identifying new opportunities & emerging technologies to implement into your business goes a long way in gaining a competitive advantage.